Contributed by VP of Processing, Scott Schiele
Following last week’s blog where we discussed base issues with stockpiles, this week we’re discussing another problem with inventory management: Bad Data. With all of the existing technology to measure, from drones to lidar scanners, bad data can be consistent across all methods of data collection. Bad data is sometimes obvious and easy to spot, however it can also be much more subtle. At Firmatek, stockpile measurement is our business. Our technicians have a lot of experience and can spot and fix most of these issues. And if we can’t fix it, we come back and measure the site again to ensure we get it right. “Bad data” is a pretty broad term and can take on a variety of forms. Some of the typical data problems we run into are coordinate system errors, scale issues (typically drone), data with double faces (lidar issues), and not enough data collected (e.g. missing pile tops). Having good data is important; however, identifying that you have bad data is even more important because it can be worse when you think everything is accurate and it’s not.
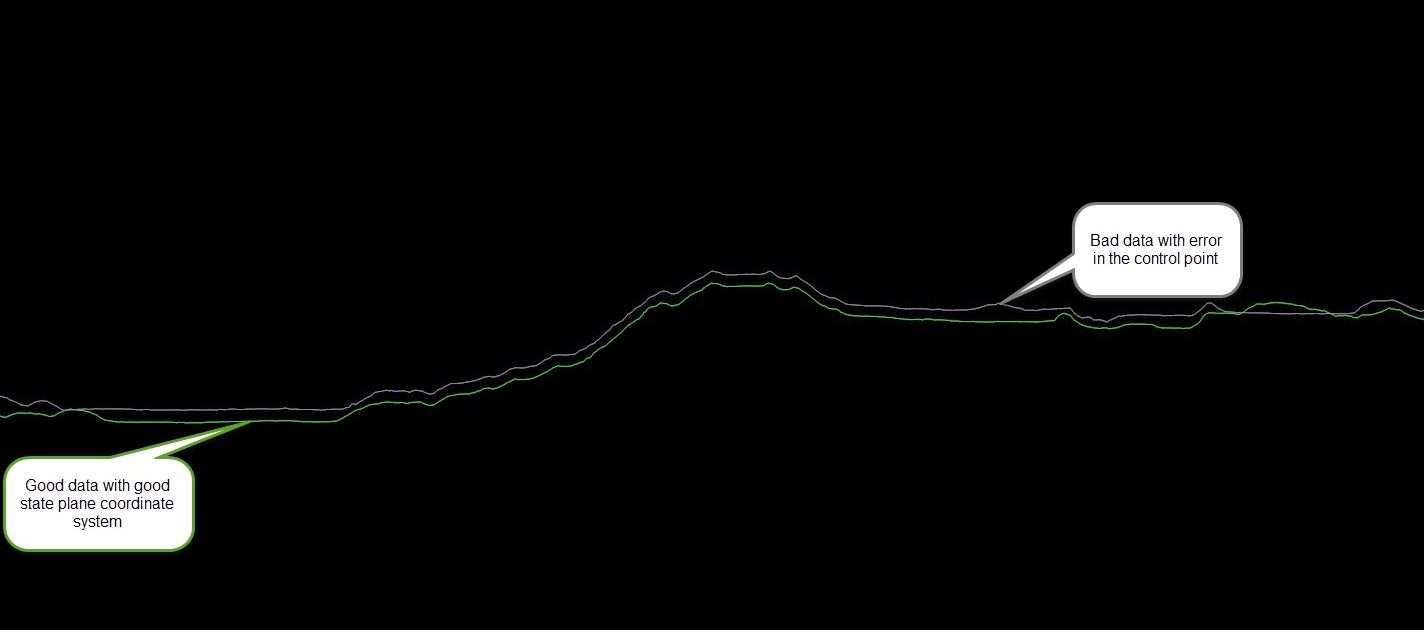
Coordinate System Errors: Coordinate systems can be simple or very complex. Without the correct coordinate system, the data does not line up with past data and is not absolutely accurate. When you are expecting absolute accuracy (the data is in the exact right spot on the earth), and you don’t get it, that can conflict with your analysis of the data. An example of when this is important is when it comes to permanent base. If the data is not in the right position, then the permanent base is not in the right position, and therefore the current data and the permanent data will not line up. This causes errors in the calculations and analysis, and therefore insights from the data. At Firmatek, we use an opus corrected state plane at each of the sites we map. This allows us to keep the coordinate system consistent and easily reproducible. At each of our sites, a technician sets a control point for our GPS system and we aim to use that point every time we are there to map the site. If base data is provided to us, it’s important that we know the coordinate system, so we can convert it correctly and ensure that this data lines up with our state plane coordinate system. When our technicians are processing data from a site, we always do checks where we compare data and make sure it lines up. Having trained eyes on the data to ensure data is lining up and in the correct spot is important to identifying issues with coordinate systems. Global Mapper is a key tool we use when fixing or re-projecting coordinates.
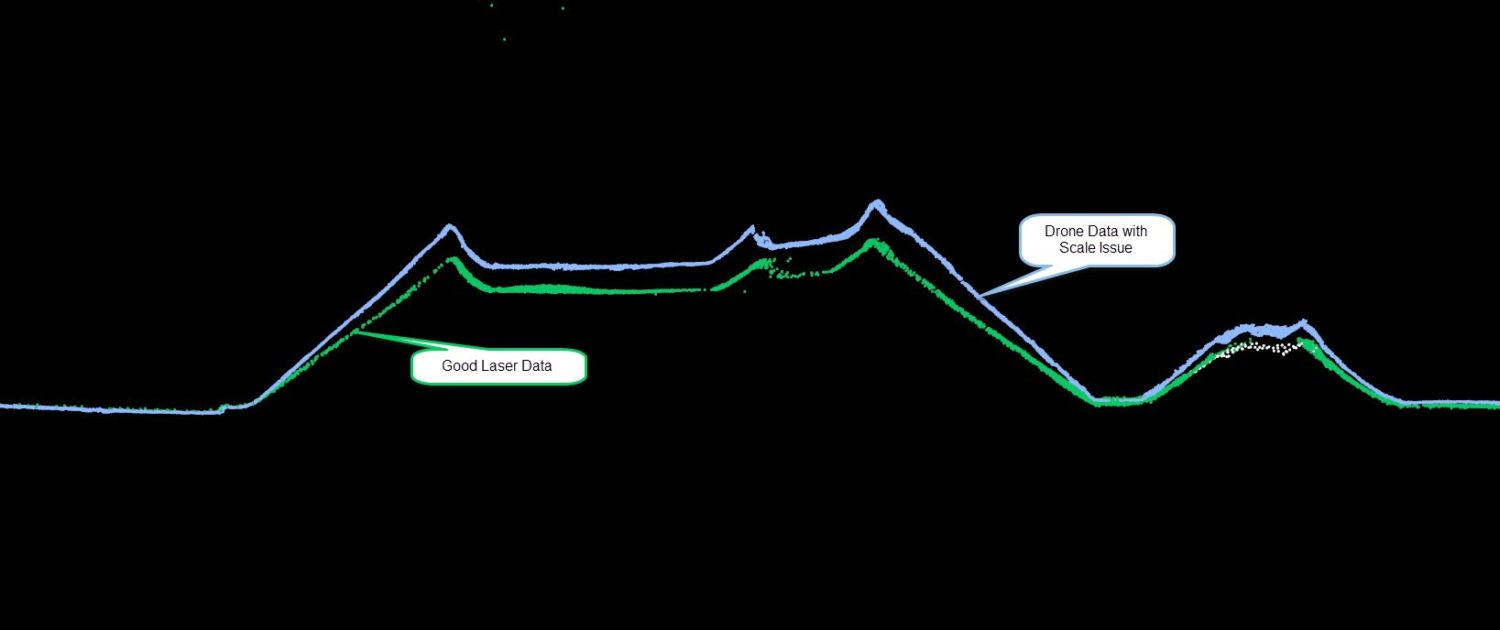
Scale Issues: We see scaling issues mostly in drone data. A scale issue is when the data isn’t scaled correctly. For example, the base of the pile is the correct length and width, but it is far taller in the data than it should be. Issues with scale can be seen in drone data and can be a challenge to detect, especially if they are small. Properly set ground control is key to a successful drone flight if you are using drone only. It is also a helpful if you have previous data to compare to your new data. If lidar data has been captured on the site, this can be helpful in checking scale. Ultimately, fixing scale issues is not always possible and sometimes can result inthe need to re-fly the site. As always, having data-trained eyes looking at these issues is very helpful.
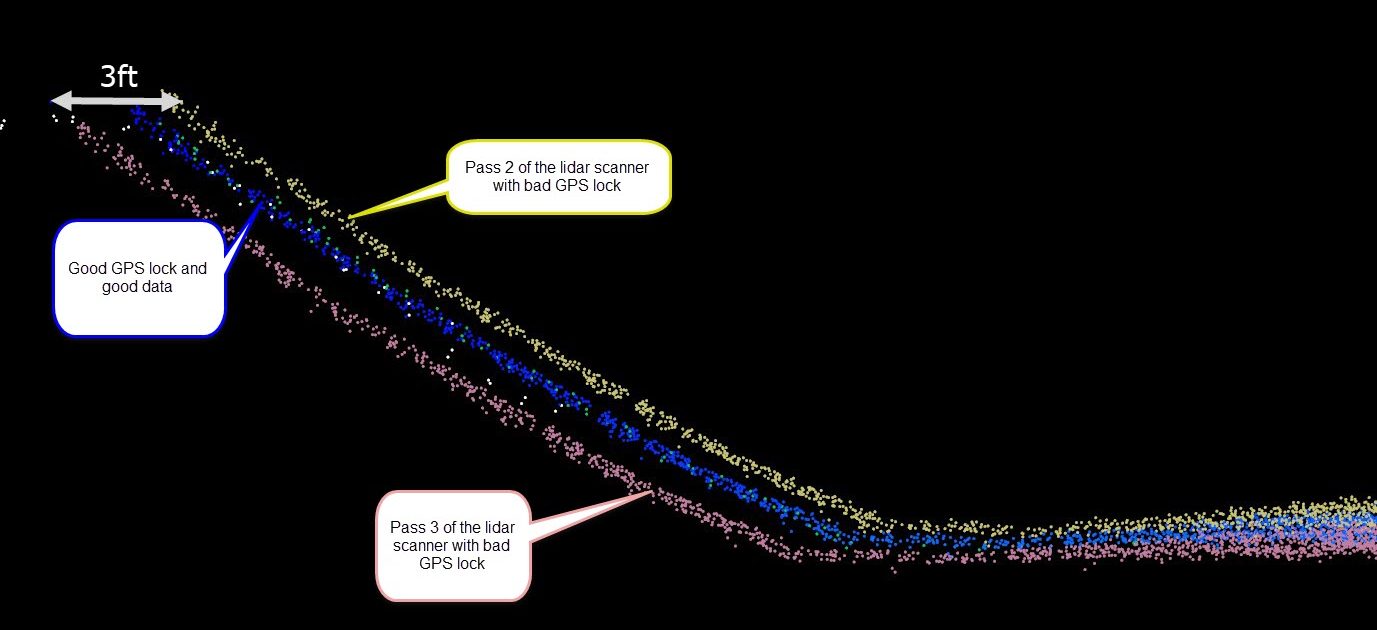
Double Faces: Double faces means that there are two sets of points over the same face of the pile or area you are scanning. When double faces appear in lidar data, it typically means that the GPS tracking on the lidar unit went out temporarily or was not accurate. One key to fixing this issue is finding when the GPS tracking went out and cleaning that data out of the point cloud. If your lidar data is excessively bumpy, this could also be a sign that the data is not accurate. In that case, it’s best to rescan this site to ensure accurate positions on the lidar data.
Missing Data: Sometimes, we don’t get data that covers the entire area that we need to analyze and calculate. If the pile is incomplete with data, no matter if it is drone data or lidar, typically the easiest fix is to go collect more data. Pile tops are a hard thing to measure when using a truck mounted lidar. Using the combination of truck mounted lidar and a drone and then merging the two data sets is a quick, accurate, and complete way to measure stockpiles. Having more than one tool on a site is often a very important. Many sites need different types of equipment to measure all the piles. Whether it’s a pile inside a shed or a pile that cannot be driven all the way around, Firmatek realizes that different tools are needed for different jobs. Our technicians are deployed with a laser scanner and drone to be as complete as possible when on a site. Some of our lasers are stop-and-go and can be easily mounted to a tripod and taken inside or around the back of a pile, while some of our lasers are vehicle mounted only. We have come across many challenges when measuring piles but rest assured, Firmatek has the tool to get the job done.
Bad data leads to incorrect insights. The only way to know if these elements are present in the data is to have a trained technician review all aspects of the data. At Firmatek, before we report stockpile volumes or deliver any mapping product to our clients, we always make sure to compare all current data to our past surveys, to be sure none of these problems exist. This gives us confidence that what we are reporting back to our clients is accurate. It also gives our clients confidence in the insights they receive from the data that they use to make decisions in their business everyday.